스마트팩토리, 창의적인 일에 집중하는 ‘사람 중심의 일터’로 변화시켜
포스코, 중소기업 혁신성장 지원 위해 오는 2023년까지 총 200억원 출연
최정우 회장, “중소기업에 스마트팩토리 지원해 산업생태계 경쟁력 제고 적극 나설 것” 다짐
문재인 대통령이 9일 국내 유일의 ‘등대공장(Lighthouse factory)’인 포스코를 방문해 스마트 혁신 및 중소기업 상생협력 현장을 둘러보고 임직원들을 격려했다.
등대공장은 어두운 밤하늘에 ‘등대’가 빛을 밝혀 길을 안내하듯, 사물인터넷(IoT), AI, 빅데이터 등 4차 산업혁명의 핵심기술을 적극 도입해 세계 제조업의 미래를 혁신적으로 이끌고 있는 공장이라는 의미다. 세계경제포럼(WEF, 다보스포럼)은 지난해 7월 포스코를 세계의 ‘등대공장’으로 발표한 바 있다.
세계경제포럼은 포스코가 철강산업에서 생산성과 품질 제고를 위해 인공지능(AI) 기술을 적용하고 있고, 대학·중소기업·스타트업들과의 협력 생태계를 구축하는 등 상생을 통해 철강산업 고유의 스마트 공장 플랫폼을 구축하고 있다는 점이 등대공장 선정 배경이라고 밝힌 바 있다.
이날 행사에서는 포스코 최정우 회장 및 스마트팩토리 사업에 참여한 임직원들이 대통령과 박영선 중소벤처기업부장관 등을 안내하며, 포스코의 스마트팩토리 추진 현황을 소개했다.
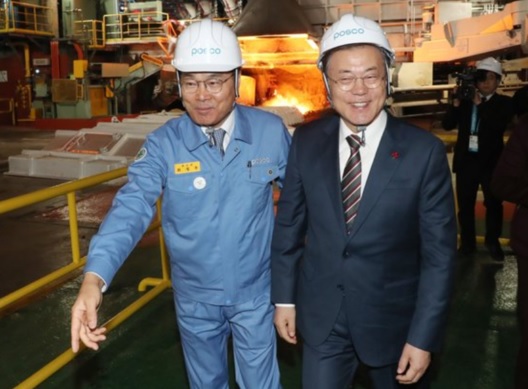
포스코는 자체 스마트팩토리 플랫폼인 ‘포스프레임’을 통해 지난 50년간 현장 경험과 노하우가 축적된 공장의 데이터를 수집, 정형화하고, 이를 스스로 학습해 최적의 공정조건을 만들어 생산과정을 실시간 제어하는 스마트 제철소를 구현해 나가고 있다고 말했다.
또 이를 통해 경험에 의존하는 수동작업을 최소화해 생산성 및 효율성 제고뿐만 아니라 안전도 향상, 단순반복 업무 저감으로 창의적인 일에 집중하는 ‘사람 중심의 일터’로 현장을 변화시키고 있다고 밝혔다.
포스코의 철강과 스마트 IT기술 융합을 위한 핵심 인프라인 ‘스마트데이터센터’를 비롯, 상생협력 추진 현황, AI기술이 적용된 최첨단 스마트 고로인 제 2고로에서 실제 쇳물이 생산되는 과정도 소개됐다.
스마트데이터센터는 포항제철소 내 공장에 설치된 사물인터넷(IoT) 센서를 통해 얻어진 빅데이터를 실시간으로 수집·저장하는 곳으로 포스코 스마트팩토리 구축의 핵심 인프라 역할을 하고 있다.
스마트고로는 딥러닝 기반 AI기술로 고로의 노황을 자동제어함으로써 기존 기술로는 개선이 어려운 원가절감, 품질향상 등에 기여하고 있다. 이를 통해 용선 1톤당 연료투입량이 4kg 감소했고 고로 일일 생산량도 240톤 늘었다. 연간 중형 승용차 8만 5천대를 생산하는데 사용할 수 있는 양이다.
포스코는 2016년부터 2019년까지 스마트팩토리 구축을 위해 321건의 과제를 수행한 결과 총 2,520억원의 원가절감 효과를 거뒀다.
이날 행사에는 상생형 스마트공장 참여 중소기업인 동국산업 안상철 대표, 종합폴스타 김철규 대표를 비롯, 포스코 스마트공장 협력중소기업인 이씨마이너 민광기 대표, 비전에스티 김중구 대표도 참석해 의미를 더했다.
포스코는 중소기업의 혁신성장을 돕고 강건한 생태계 조성을 위해 중소벤처기업부와 함께 '상생형 스마트공장 구축 지원 및 스마트화 역량강화 컨설팅' 사업을 추진중으로, 오는 '23년까지 총 200억원을 출연해 1,000개 기업을 지원할 예정이다.
‘상생형 스마트공장’의 경우 지난해 기준으로 비거래 59개사를 포함하여 총110개사에 대해 구축을 완료했고, 성과측정이 완료된 25개사를 대상으로 조사한 결과 스마트사업이 적용된 설비, 공정에서 생산성과 품질은 각각 43%와 52% 증가하고, 비용과 납기는 27%가량 줄어든 효과를 거둔 것으로 나타났다.
이날 행사에 참석한 동국산업 안상철 대표와 종합폴스타 김철규 대표는 포스코의 지원으로 구축한 표면처리 최적조건 도출 AI제어모델, 모바일 공정관리 체제를 통해 각각 생산성 60%, 매출액 35%가 증가했다고 밝혔다.
포스코의 열연코일을 소재로 자동차부품용 고합금강을 생산하는 동국산업은 포스프레임으로부터 제공받은 열연코일 제품 및 스케일(산화물) 내부 산화층 예측 정보를 기반으로 최적의 산세처리(열연강판 표면의 스케일(산화물) 등을 산을 통해 세정하는 과정) 속도를 계산해 자동제어하는 AI제어모델을 구축했다. 이후 축적된 정보는 빅데이터화되어 포스프레임에 반복적으로 저장되며 AI는 개선된 최적값을 산출하기위한 학습을 지속한다.
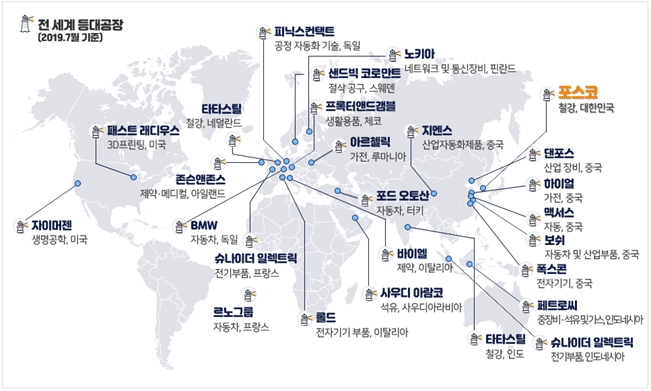
선박용 엔진 부품 재생수리 전문기업 종합폴스타는 포스코의 현장혁신활동인 QSS(Quick Six Sigma)를 도입해 원가를 절감하고 생산성을 향상시켰으며, 상생형 스마트공장 구축 지원을 통해 생산 현황 실시간 모니터링과 영업-생산간 정보공유가 가능한 모바일 공정관리 체제를 갖췄다.
최정우 포스코 회장은 “스마트 기술로 세계 최고 수준의 프리미엄 제품과 서비스를 지속 제공하고, 스마트팩토리 경험을 중소기업과 공유하고 지원함으로써 우리의 산업 생태계 경쟁력 제고에 더욱 적극적으로 나서겠다"고 말했다.
△ 포스코 스마트팩토리 사업의 컨트롤타워 ‘스마트데이터센터’
포스코는 지난 2018년 포항제철소에‘스마트데이터센터’를 가동해 공장 스마트화에 한 발 더 다가섰다.
스마트데이터센터는 포항제철소 내 공장에 설치된 사물인터넷(IoT) 센서를 통해 얻어진 빅데이터를 실시간으로 수집·저장하는 곳으로 포스코가 추진하는 스마트 팩토리 사업의 컨트롤타워 역할을 하는 핵심 인프라다.
스마트데이터센터에 모아진 공장의 각종 정보들은 포스프레임에 축적되고 이를 통해 분석하고 예측한 정보를 바탕으로 포스코는 현장에서 최적의 생산 환경을 구축하게 된다.
총 1년 3개월간의 공사기간을 거쳐 완공된 스마트데이터센터는 총 2550㎡(772평) 부지에 3층 규모로 지어졌으며 외관은 데이터센터 이미지에 맞게 ‘QR 코드’로 형상화했다.
1층에는 전기실, 비상발전기실, 공조 기계실 등 기반설비를 설치했으며, 2층과 3층은 서버, 스토리지, 네트워크장치 등 최신 IT 설비와 관제시설을 배치했다.
건축물에는 포스코의 월드탑프리미엄(WTP) 제품이 적극 사용됐다. ‘녹슬지 않는 철’로 유명한 포스맥을 비롯해 고강도 강관파일, 성능 향상형 합성골조 등이 적용됐다.
스마트데이터센터는 연중 24시간 운영되며 지진, 화재 등 각종 재난으로부터 IT장치를 보호하기 위해서 진도 8.0의 지진에도 끄떡없는 면진설비 (지반과 건물 사이에 고무 블록 및 베어링 등 면진장치를 설치해 지반으로부터 전달되는 지진력을 감소시키는 설비)를 갖췄다. 또한 첨단 소화설비도 설치해 화재 시 초기에 신속하게 진화할 수 있도록 했다.
건물 외벽에는 포항산업과학연구원(RIST)에서 연구개발한 컬러 건물일체형 태양광발전 (BIPV ; Building Integrated Photovoltic) 설비를 적용했고 냉방설비도 외부 기온에 따라 연동돼 에너지절감 효과를 높였다.
포스코는 올해 상반기 내 광양제철소 스마트데이터센터를 가동할 예정이다.